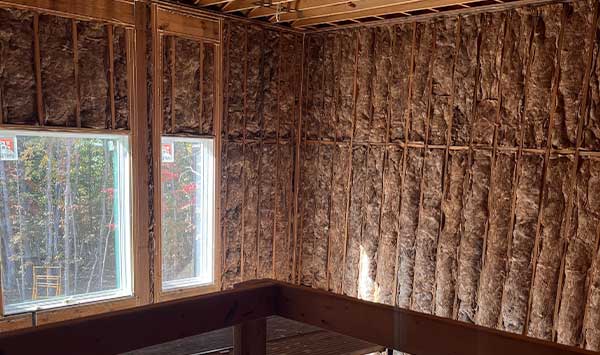
Don’t let future homeowners’ hard-earned money escape through the cracks! In Virginia’s diverse climate, home air sealing is a crucial investment for anyone building a new house. Properly sealing your home building project improves the comfort, energy bills, and indoor air quality for future residents, while also reducing the home’s environmental impact. So, take the time now, during construction, to properly air seal your new home building project.
Air sealing involves closing gaps, cracks, and holes in the building envelope to create an air barrier that prevents unwanted airflow. At Toler Insulating, as experts in building science and the building of energy-efficient homes, we understand the unique challenges and opportunities in Virginia’s construction market. Let’s dive into the priority air sealing locations that will make your new home project as efficient as possible.
Five Priority Air Sealing Locations
Air sealing your home building project before installing insulation is one of the most effective steps towards building an energy-efficient house. Take the time to prioritize these five key areas as you air seal and help your home project meet International Energy Conservation Code (IECC) and state residential energy code standards.
Location #1: Top Plate to Attic Drywall
The top plate to attic drywall is one of the most critical air sealing priorities and can provide the greatest impact of all five locations we mention. Warm air naturally rises, making this area prone to air leaks. Proper sealing here involves using high-quality caulk or foam sealant and ensuring complete coverage.
Coordinating with insulation installation is essential to avoid gaps. Different roof designs and framing methods can affect how you seal this area, but a properly air sealed top plate significantly reduces energy loss and improves airtightness requirements compliance.
Location #2: Recessed Lights
Even though most recessed light fixtures are labeled airtight, it’s imperative that they are sealed to the sheetrock or protected with an airtight cover. Improperly sealed recessed light fixtures can create significant leakage points, costing future homeowners valuable money. To address this, use airtight, IC-rated (insulation contact) fixtures. Sealing around these lights with either gaskets or caulk ensures minimal energy loss.
While airtight housings are ideal for new installations, existing fixtures can be sealed with caulk or gaskets. Each method has pros and cons, but all contribute to meeting energy efficiency codes.
Location #3: Band Joist
The band joist areas, located where the foundation meets the framing and at the top of the wall, are another critical area. These locations are prone to air leaks and if overlooked they can leave over 200 feet of air leaks. Sealing these areas effectively requires materials like spray foam insulation, which provides both thermal resistance and airtightness.
Different construction types may call for varied approaches, but sealing the band joist areas is a non-negotiable for builders serious about taking steps to reduce air leakage and achieve airtightness requirements.
Location #4: Windows and Doors
Energy-efficient windows and doors with proper seals are essential for building energy efficiency. Use low-expansion foam and weatherstripping during installation to ensure an airtight fit.
All windows and doors are not created equal, so it’s important to choose the right materials and installation techniques to ensure your home building project is properly air sealed against the elements. You may also consider utilizing house wraps and window flashing to help create a comprehensive air barrier.
Location #5: Ductwork
Leaky ductwork can undermine the energy performance of even the most energy-efficient homes. Sealing around the duct and duct boot with mastic sealant where they meet is crucial for maintaining airtightness.
You can test your ductwork with duct tests, such as blower door tests, to identify problem areas, ensuring your duct boot and other components are sealed to prevent energy loss and maintain indoor air quality.
Beyond the Basics: Advanced Air Sealing Considerations
Whole-Building Approach
Instead of compartmentalizing, take a comprehensive, whole-building strategy to address all potential leakage points in your project’s building envelope. This includes crawl spaces, attics, and other less obvious locations for new homes.
Building Science Principles and Advanced Techniques
The building science principles of air flow, heat flow, and moisture flow, guide effective air sealing strategies by addressing thermal bridging, moisture control, and pressure differentials. By controlling these things, you can ensure long-term durability and efficiency of your newly constructed building.
When air sealing, you may also want to consider advanced air sealing techniques such as spray foam insulation. This expanding material excels at filling irregular gaps but must be installed correctly to avoid moisture issues.
Your Partner for an Energy-Efficient Home
If you’re building a new home in Virginia, take time to prioritize air sealing the five key areas we mentioned: top plates, recessed lights, band joists, windows and doors, and ductwork. At Toler Insulating, we prioritize quality service and customer satisfaction. We’re here to help you navigate energy efficiency codes and achieve a properly sealed, energy-efficient home building project. Contact us today for a free consultation on home air sealing and insulating your Lynchburg building project.
For an even more in depth look at our topic, check out this video featuring our founder Wayne Toler and Builder Eddie Fort of PD&M General Contractors. Have questions about your building project? Contact Us—we’d love to hear from you!
Have questions about your building project? Contact Us—we’d love to hear from you!